S.N 14 - Henan Shuanghui Food
Project location: Henan, Luohe
Equipment selection:
1453KW steam fired LiBr absorption chiller
1453KW hot water LiBr absorption chiller
930KW hot water LiBr absorption chiller
Main function: Utilize high-temperature steam condensate from recycled food disinfection as power to provide process cooling and plant air conditioning
General introduction
To ensure the stability of the cooling capacity of the hot water LiBr absorption chiller and effectively manage the fluctuating temperature and flow rate of the high-temperature sterilizing water, using a plate heat exchanger for indirect heat exchange from the circulating hot water tank is a suitable solution. Below is a general description of the possible technical parameters for a plate heat exchanger used in this setup:
Plate Heat Exchanger Technical Parameters
- Heat Transfer Area: This parameter is critical for ensuring that enough surface area is available for heat exchange between the hot water and the LiBr absorption chiller. Typically, the required heat transfer area can be estimated based on the thermal load of the absorption chiller and the temperature differences across the plates.
- Example: 50-100 m² (depending on the required cooling capacity).
- Flow Rate: The plate heat exchanger must handle the fluctuating flow rates from the circulating hot water tank and sterilizing water. The flow rate parameters must be capable of accommodating a range of 140 m³/h for circulating hot water and 20-100 m³/h for sterilizing water.
- Example: Max flow rate of 150 m³/h for hot water input.
- Operating Temperature Range: The temperature range of the incoming hot water from the sterilizing process is between 105°C and 115°C, while the temperature of the circulating hot water tank is between 95°C and 99°C. The heat exchanger must handle these variations and maintain efficient heat transfer.
- Example: Hot side temperature range: 105°C - 115°C
- Cold side temperature range: 95°C - 99°C
- Plate Material: The material of the plates should be corrosion-resistant to handle high temperatures and possible chemical exposure in the hot water system.
- Example: Titanium or stainless steel (304 or 316) for corrosion resistance.
- Pressure: The plate heat exchanger should be designed to withstand the operating pressure of the system.
- Example: Maximum operating pressure: 10 bar (or higher based on system requirements).
- Connection Size: The inlet and outlet sizes of the heat exchanger must align with the pipe sizes used in the circulating hot water tank and sterilizing water system.
- Example: Inlet/outlet pipe size: DN150 or DN200 depending on the flow rate.
- Heat Transfer Coefficient: The heat exchanger should be designed for optimal heat transfer performance based on the properties of the fluids.
- Example: Typical heat transfer coefficients can range from 500-800 W/m²·K, depending on fluid velocity and temperature differences.
- Design Pressure Drop: The pressure drop across the heat exchanger should be minimized to ensure efficient operation and to prevent excessive load on the pumps.
- Example: Pressure drop: 1-3 bar.
- Compactness: Plate heat exchangers are known for their compact design, which is important in industrial applications with limited space.
- Example: Compact design with modular plates for easy scalability.
These parameters are indicative and may vary based on the specific heat exchanger manufacturer and system requirements. Further customization may be necessary based on detailed engineering analysis to match the exact operating conditions and system integration.
To design an efficient heat exchange system that satisfies the given parameters for the plate heat exchanger and maintains the required temperatures and flow rates, let's summarize and refine the conditions based on the provided information:
System Overview and Technical Details:
1# Plate Heat Exchanger (Preliminary Heat Exchange)
- Primary side (Hot Water)
- Inlet Temperature: 97°C
- Outlet Temperature: 87°C
- Flow Rate: 100 m³/h
- Secondary side (Cold Water/Chiller Input)
- Inlet Temperature: 78°C
- Outlet Temperature: 87°C (which returns to the hot water tank)
The primary side of the heat exchanger exchanges heat with the secondary side to raise the secondary side outlet temperature to 87°C. This temperature of 87°C is then returned to the hot water tank.
Process for Raising the Inlet Temperature of the Hot Water LiBr Absorption Chiller:
- Objective: The aim is to increase the inlet temperature of the hot water LiBr absorption chiller by using the heat from the 87°C secondary side.
- Solution: The outlet water at 87°C from 1# plate heat exchanger (secondary side) is redirected to 2# plate heat exchanger to further exchange heat.
2# Plate Heat Exchanger (Temperature Boosting)
- Primary side (Hot Water)
- Inlet Temperature: 110°C (driven by high-temperature sterilizing water from the process)
- Outlet Temperature: 95°C (leaving the heat exchanger after exchanging heat with the secondary side)
- Secondary side (Hot Water LiBr Chiller Inlet)
- Inlet Temperature: 87°C (from the 1# plate heat exchanger outlet)
- Target Outlet Temperature: 92.4°C (desired temperature to feed into the LiBr absorption chiller)
Heat Exchange Process:
- The primary side in 2# plate heat exchanger delivers water at 110°C to heat the secondary side, which receives water at 87°C from the 1# plate heat exchanger.
- Heat is transferred between the two sides, raising the secondary side outlet temperature from 87°C to 92.4°C before it is sent to the LiBr absorption chiller.
Updated Process Flow:
- The primary side of 1# plate heat exchanger starts with hot water at 97°C (inlet) and cools it to 87°C (outlet), which is returned to the hot water tank.
- The secondary side of 1# plate heats up water from 78°C to 87°C.
- The 87°C water from the 1# plate is now fed to the primary side of 2# plate, where it is heated by the 110°C input from the sterilizing water system.
- The water then flows to the secondary side of 2# plate, where it is heated further to 92.4°C before being sent to the hot water LiBr absorption chiller.
Key Considerations for Plate Heat Exchanger Design:
- Thermal Load: The heat exchange between the two plates should be designed for the temperature difference, ensuring that the heat from the 110°C primary side effectively raises the 87°C secondary side water to the desired 92.4°C.
- Flow Rates: The secondary flow rate of 111 m³/h and the primary flow rate of 100 m³/h need to be balanced to maintain the heat transfer efficiency without causing excessive pressure drop or uneven heat distribution.
- Heat Transfer Efficiency: The heat exchanger plates should be designed to handle the specific heat transfer required between the hot sterilizing water and the cooling water, ensuring the target temperature of 92.4°C is achieved efficiently.
This process layout ensures the efficient use of waste heat to raise the temperature for the LiBr absorption chiller while maintaining stable and optimized operation.
Web: https://www.deepbluechiller.com/
E-Mail: yut@dlhope.com / young@dlhope.com
Mob: +86 15882434819/+86 15680009866
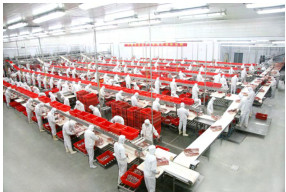
Post time: Mar-30-2023