Effect of Fouling Factor of Cooling Capacity
The Impact of Fouling on LiBr Absorption Units
Hope Deepblue, a trusted expert in LiBr absorption chillers and heat pumps, emphasizes the importance of professional maintenance in ensuring the long lifespan and efficiency of its units. Despite their reliability, prolonged operation can lead to fouling in the pipeline, which significantly impacts the performance of these systems.
Understanding Fouling and Its Effects
Fouling refers to the accumulation of dirt, scale, and other deposits on the inner walls of heat exchange tubes. This buildup is quantified by the fouling factor, a measure of thermal resistance caused by the fouling layer.
- Increased Thermal Resistance: As fouling develops, it impedes heat transfer by acting as an insulating barrier.
- Reduced Heat Transfer Efficiency: The diminished ability to transfer heat leads to a notable drop in the cooling capacity of the unit.
- Operational and Energy Losses: The decreased cooling capacity results in reduced system performance and increased energy consumption.
The Importance of Maintenance
To combat the effects of fouling, regular maintenance and cleaning are essential. By addressing fouling issues proactively, Hope Deepblue ensures that:
- Cooling Capacity is preserved for efficient operation.
- Energy Efficiency remains high, reducing operational costs.
- System Lifespan is extended, protecting the investment in advanced HVAC solutions.
With a focus on preventive care, Hope Deepblue supports its clients in maintaining optimal performance, ensuring that their units continue to deliver the reliable cooling and heating they were designed for.
The Impact of Water Quality on LiBr Absorption Unit Performance
Hope Deepblue emphasizes the critical role of water quality in maintaining the efficiency and longevity of LiBr absorption chillers and heat pumps.
Factory Testing vs. Sample Data
During factory testing, the internal water-side pipes of the unit are meticulously cleaned, resulting in a lower fouling factor of 0.043 m²·°C/kW. In contrast, the performance data provided in product samples typically assumes a fouling factor of 0.086 m²·°C/kW, reflecting real-world conditions. This difference explains why the cooling capacity during factory tests is higher than that indicated in the sample data.
Consequences of Poor Water Quality
The fouling factor increases when impurities accumulate on the inner surfaces of the heat exchange tubes, leading to:
- Decreased Heat Transfer Efficiency: Fouling acts as an insulating layer, hindering thermal conductivity and reducing cooling capacity.
- Corrosion Risks: Contaminants in poor-quality water can cause corrosion, impacting the operational stability and shortening the lifespan of the unit.
- Exacerbated Fouling in Direct-Fired Units: In systems where hot and cold water share pipelines, higher water temperatures intensify dirt formation, compounding fouling and efficiency losses.
Ensuring Optimal Performance
To combat these challenges, maintaining high-quality water is essential. Recommended measures include:
- Regular water treatment to remove impurities and prevent scaling.
- Implementing preventive maintenance to clean and inspect the system periodically.
- Monitoring water chemistry to minimize conditions conducive to fouling and corrosion.
By prioritizing water quality, Hope Deepblue ensures its units deliver reliable performance and long-term operational excellence.
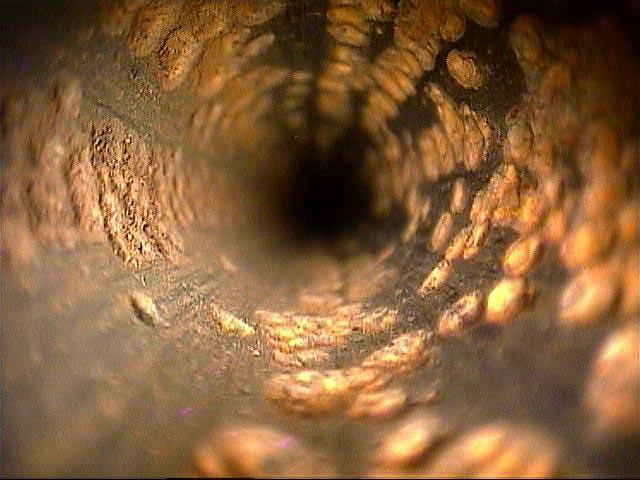
Post time: May-30-2024